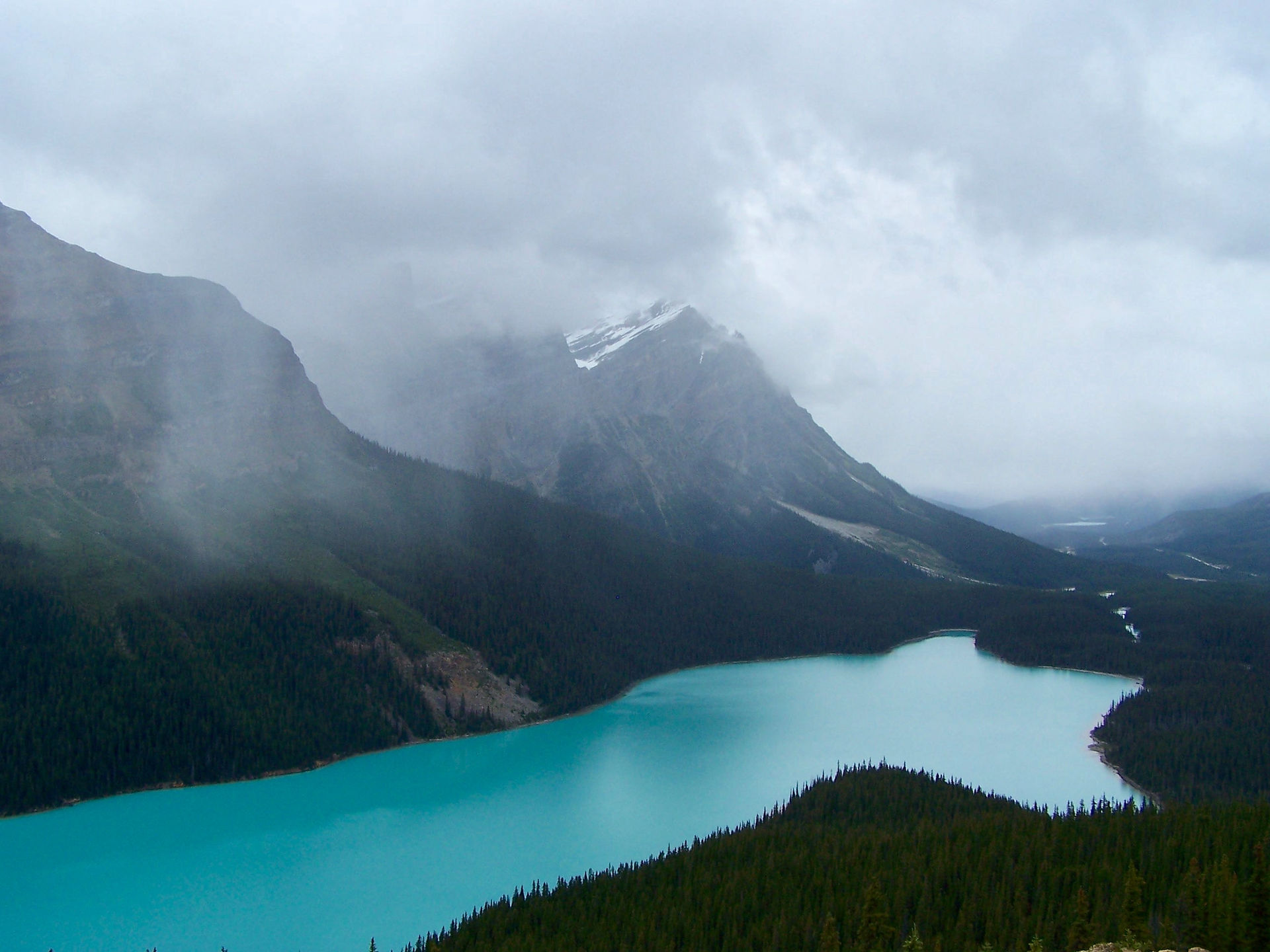
Jonathan Balash, P.Eng.
BSc in Mechanical Engineering with Distinction, University of Alberta
OMEGA
Enbridge EIM, 2018-2023
Enbridge is entering a new era of engineering information management. I had been contracted out to work as a project analyst for the Optimized Management of Engineering Geographical Assets (OMEGA) project.
​
This project has the goal of centralizing asset data into a GIS where users can obtain data through a map interface. My role in the project is comprised of populating spreadsheets with the required data, validating the data against records, and also performing QA/QC checks on completed work.
​
I have had to overcome many challenges since starting on this project including learning about GIS and geospatial referencing, how to work efficiently with large data sets in MS Excel, and learning two new software packages. Overcoming these challenges has both refined my skills as they pertain to mechanical engineering and broadened my skill set to include other relevant disciplines.

RFID Pet Dish
Home Project, 2021
My family had recently adopted a second cat, but there was tension in the air. The new cat was eating all of the other cat's food. Of course, there are pet food dishes on the market that are able to protect our first cat's food, but with an Arduino UNO sitting on my desk, I decided to try my hand at designing and building one of my own with my newly acquired 3D printer.
​
The design process lasted about a week during my spare time. I went through multiple revisions in Solidworks before I was happy with both the aesthetics and size of the device. Throughout the design process, I also had to figure out what electric components I would need, wire routing and what off the shelf mechanical components I would use, all while considering the limits of my 3D Printer.
​
Once I was happy with the design, I performed a couple test prints of critical areas (PCB mounting points, threaded insert holes) to make sure I had proper tolerances accounted for before I committed to printing the entire project. Once everything was printed, assembly and programming began. I had 3 major requirements, the food dish had to open when the cat was near the dish, and close shortly after to avoid food theft, I needed a battery level indicator to tell me when to swap out the Milwaukee m12 battery, and I wanted to get multiple days of battery life. Furthermore, I wanted the dish to open and close as a test cycle to show that it was working whenever I powered it on. I was able to meet all of these requirements with 2 weeks of R&D, along with winding my own custom antenna to use with the RFID reader board to extend its range.
​
With a week of training, the cat was regularly using the food dish. Peace was finally achieved between the two cats, until the new cat found out he could sneak in immediately after the other cat and as long as he kept his head in the dish, he would not allow the mechanism to close.
​
Rev 2 coming soon . . .


Modufill Automated Bottle Filling Station
Capstone Project, 2017
My capstone project involved designing an automated bottle filling station that followed Industry 3.0 standards. This project was completed with a group of four mechanical engineering students which resulted in the concept seen to the right.
​
The design features two modules, the first module is used for filling and capping the bottles, while the second module (from left to right) is used for storing bottles. Since these modules are meant to be part of an assembly line, they have been designed with adaptability in mind.
​
Components of the project include a cost analysis to compare with the client provided budget, performing a structural analysis of the mechanisms involved, as well as research relevant safety and operational standards. Project management was also a key portion of the capstone project.

Remote Controlled Quadcopter
Design for Manufacture Course Project, 2017
The focus of this project was to integrate DFMA (design for manufacture and assembly) ideologies into the design of a mechatronic device. Throughout the project, the four of us learned the strengths and weaknesses of various manufacturing methods. The manufacturing methods available to the group were additive manufacturing via FDM, laser cutting of acrylic sheets, water jet cutting of carbon fiber, PCB manufacture and traditional machining operations.
​
Unfortunately the assembly did not go as well as planned due to the limitations in fastener availability and underestimating the space required for wiring. In spite of this, it was a fantastic learning experience that taught me how to tolerance for a manufacturing process, select a manufacturing method for a specific material or tolerance requirement, and also how to design for easy assembly. The project also focused on teaching us about geometric dimensions and tolerances, and their advantages over traditional dimensions and tolerances. This dimensioning scheme was used for the required drawing package.

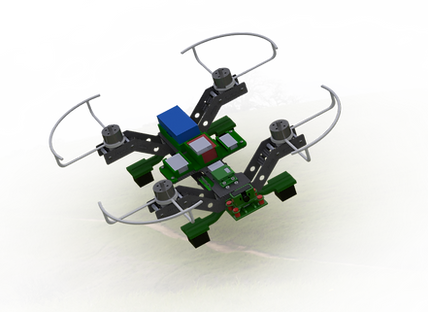